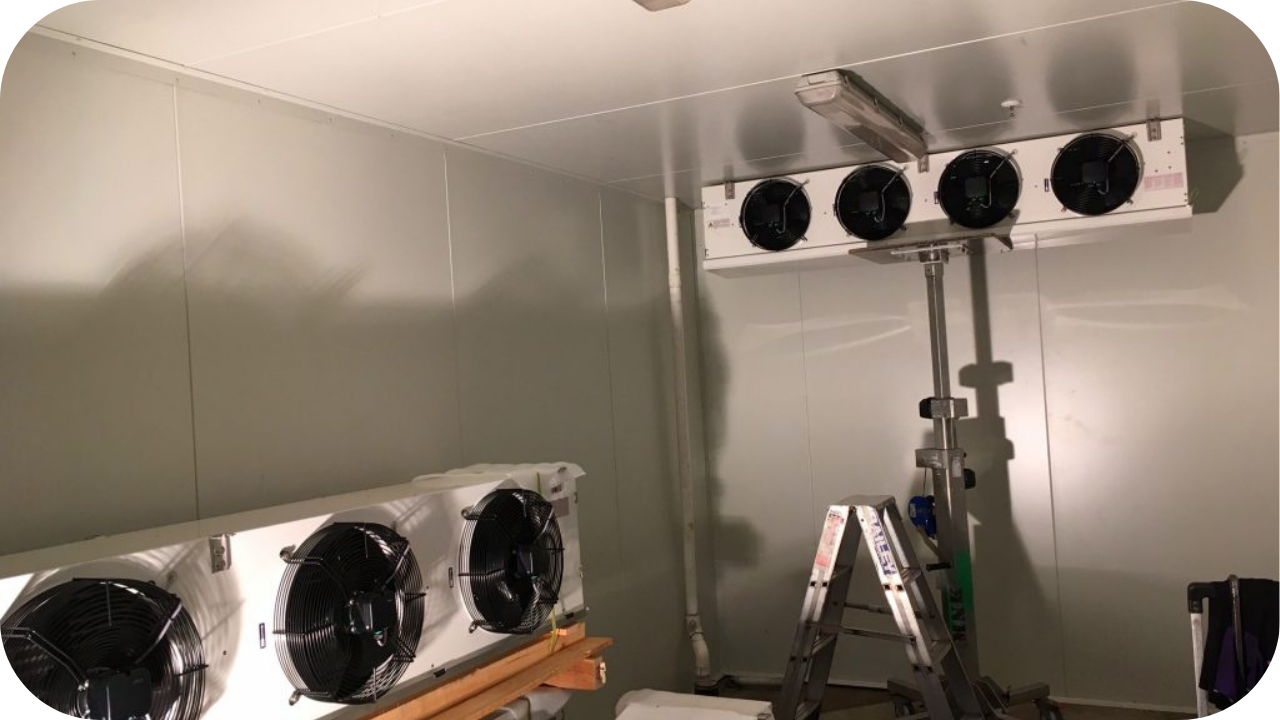
A failing cool room can cost you thousands in spoiled stock. One day, everything seems fine. Next, your cooling system struggles to maintain the right temperature, and you’re left scrambling.
Ignoring the warning signs can lead to breakdowns, wasted food, and higher power bills. But how do you know when your cool room needs attention? Some issues are obvious, like strange noises or warm air. Others are subtle, creeping up until they become a major problem.
Let’s break down the telltale signs that signal trouble. Catch them early, and you’ll save money, avoid disruptions, and keep your business running smoothly.
Why Regular Cool Room Maintenance Is Crucial
Cool rooms run non-stop. Any minor issue can quickly become a major headache. A well-maintained system keeps food fresh, saves energy, and prevents sudden breakdowns.
Ignoring small signs of failure can lead to spoiled stock, higher running costs, and costly emergency repairs. A fluctuating temperature can ruin perishable goods, while faulty components force the system to work harder, leading to expensive power bills. When minor issues go unnoticed, they escalate into full breakdowns that can cost thousands to fix.
Regular servicing helps detect problems early. It ensures your cool room stays efficient, reliable, and cost-effective. Before looking at when to call for help, let’s go over the most common warning signs.
Warning Signs Your Cool Room Needs Repair
Trouble often starts small before turning into a costly breakdown. Watch out for these warning signs before it’s too late.
1. Inconsistent Temperature or Poor Cooling Performance
A cool room should maintain a steady temperature. If you notice fluctuations, something’s wrong. Warm spots inside the unit can mean failing components, while sudden temperature drops might signal sensor issues.
Faulty thermostats often send incorrect signals, causing cooling delays. Refrigerant leaks reduce cooling power, making it harder for the system to maintain consistent temperatures. Blocked airflow due to dust and debris clogging vents can also reduce efficiency.
A failing cooling system forces compressors to work harder, increasing energy use. If your cool room struggles to hold the right temperature, don’t ignore it. Left unchecked, it can lead to complete failure.
2. Excessive Ice or Frost Build-Up
A layer of frost inside the cool room isn’t always a problem. However, excessive ice on shelves, walls, or the evaporator coil means trouble.
Damaged door seals allow warm air to seep in, creating condensation that freezes. Blocked air vents restrict airflow, leading to moisture build-up. If the defrost system fails, ice keeps forming instead of melting as it should.
Too much frost forces the unit to work harder, leading to higher electricity bills and potential system failure. If you notice thick ice forming, it’s time to act.
3. Strange Noises Coming from the Unit
Cool rooms are designed to run quietly. If you start hearing humming, buzzing, or rattling, something isn’t right.
Loose components can create rattling sounds due to vibrations from worn-out parts. Refrigerant issues often cause gurgling or bubbling noises, indicating a possible leak. Motor problems, such as a failing fan motor, can result in grinding or squealing sounds.
Unusual noises often indicate mechanical stress. If left unchecked, they can lead to system failure. If your cool room sounds different from usual, call a technician before the damage worsens.
4. Increased Energy Consumption or High Electricity Bills
Has your power bill suddenly spiked? A struggling cool room consumes more energy to maintain the right temperature.
Dirty condenser coils accumulate dust, reducing cooling efficiency. Poor insulation allows warm air to enter, making the system work harder. A failing compressor forces the unit to run longer than necessary, using more power.
An inefficient cool room can cost you hundreds more in electricity each month. If your bill has increased without explanation, your system may need urgent attention.
5. Water Leaks or Excess Condensation
Water should never pool inside or outside your cool room. If it does, something is wrong. Blocked drain lines trap dirt, preventing proper water drainage. Damaged seals allow warm air to enter the unit, creating condensation. Faulty humidity control can cause excessive moisture to form inside.
Leaking water can cause electrical damage and encourage mould growth. If you notice damp spots, fix them fast to avoid further damage.
6. Unpleasant Odours Inside the Cool Room
A well-maintained, cool room should smell neutral. If you detect musty, rotten, or chemical-like odours, don’t ignore them.
Mould and bacteria growth often result from high humidity or poor ventilation. A chemical smell can indicate a refrigerant leak, which may pose a safety risk. Spoiled stock inside the unit can also release foul odours, signalling improper cooling.
Bad smells often signal deeper issues. If a quick clean doesn’t solve the problem, it’s time for a check-up.
7. Doors Not Sealing Properly
Doors that don’t close fully allow cold air to escape. Even a small gap forces the system to work harder.
Cracked or worn door seals allow warm air inside, reducing efficiency. Misaligned hinges prevent doors from shutting flush, causing cooling performance to drop. Weak latches stop the door from sealing tightly.
A simple test can help. Place a piece of paper in the door and close it. If you can pull the paper out easily, the seal isn’t tight enough.
What Happens If You Ignore These Signs?
Delaying cool room repairs can lead to major problems. Even a small temperature fluctuation can ruin stock. A faulty system works overtime, increasing energy bills. If left unchecked, minor issues can turn into complete system failures that demand expensive emergency repairs.
Ignoring warning signs also affects food safety. If perishable goods are stored at the wrong temperature, bacteria can grow, leading to contamination. In industries like hospitality and food retail, this could result in health violations, loss of customer trust, and potential legal consequences.
Mechanical strain is another issue. When components like compressors or fans struggle to compensate for inefficiencies, they wear out faster. This leads to more frequent breakdowns, higher maintenance costs, and a shorter lifespan for your cooling unit.
Equipment downtime can also disrupt business operations. If a cool room fails unexpectedly, you may need to shut down until repairs are complete, causing financial losses. Fixing problems early saves money and prevents disruptions. If you’ve noticed any of these warning signs, don’t wait.
When Should You Call a Professional Cool Room Technician?
Some minor issues, like cleaning vents or checking door seals, can be handled in-house. But serious problems need expert attention.
If your cool room struggles to stay cold, produces excess frost, leaks water, or makes strange noises, it’s time to call a technician. A sudden spike in energy bills without any changes in usage is another red flag.
Regular servicing prevents costly repairs and ensures your unit runs at peak efficiency. If something feels off, getting it checked now can save you from a costly breakdown later.
Preventative Maintenance Tips to Avoid Costly Repairs
Routine maintenance keeps your cool room running smoothly. Simple steps can extend its lifespan and reduce the risk of failure.
- Clean condenser coils and vents: Dust buildup restricts airflow, making the system work harder and reducing efficiency. Regular cleaning prevents overheating and strain on the compressor.
- Check door seals regularly: Worn or damaged seals allow cold air to escape, forcing the unit to work overtime. Inspecting and replacing faulty seals helps maintain optimal cooling.
- Monitor for leaks and unusual noises: Water leaks, frost buildup, or strange sounds can indicate early-stage problems. Identifying these issues early prevents costly repairs.
- Maintain proper airflow: Ensure vents and air circulation areas are clear of obstructions. Blocked airflow reduces cooling performance and can lead to temperature inconsistencies.
- Schedule professional servicing: A trained technician should inspect the system every six to twelve months to check refrigerant levels, test components, and ensure everything is running efficiently.
Conclusion
Catching cool room problems early can save you money, prevent stock loss, and avoid major breakdowns. If you notice fluctuating temperatures, high energy bills, leaks, or strange noises, don’t wait. A small fix today can prevent a costly repair tomorrow.
Need expert help? Mercer Refrigeration Pty Ltd provides professional repairs and maintenance to keep your cool room running efficiently. Get in touch today for a fast and reliable solution. Call now or book an inspection to prevent costly downtime!